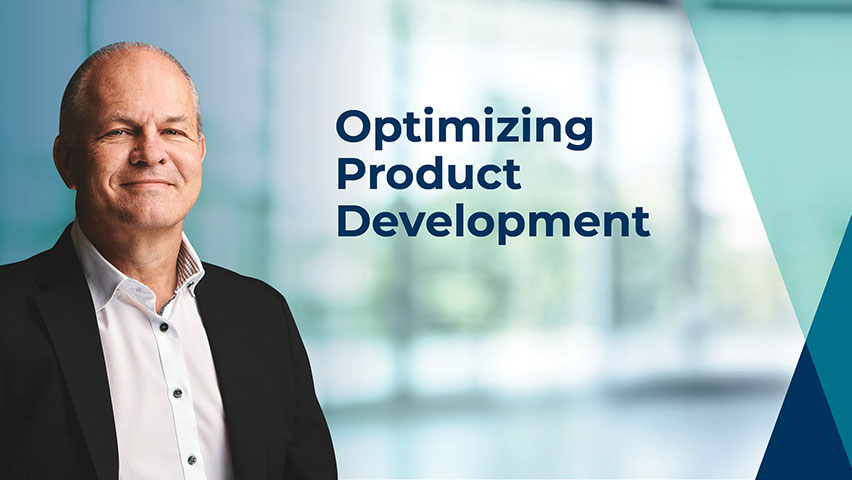
As Chief Technology Officer (CTO) and Senior Vice President Electronics & Software, I am responsible for product engineering and seek to understand and anticipate consumer and market trends, assess the potential together with the HBK business segments, and then work with the development teams to form a technology strategy to drive state-of-the-art solutions that will help our customers innovate, faster.
While there are several current and underlying trends affecting product development, the standout feature has been the investment in software and simulation to left shift product development and in some cases completely disrupt the business model. COVID-19 has acted as an accelerant for advancements, which would otherwise have happened over the next decade. Take, for example, products or businesses such as Zoom or Cinch. Microsoft® is a great example of pushing the envelope and creating an eco-system around tools like Teams.
The automotive market is going through a transformation of the century via the so-called ACES (Autonomous, Connected, Electric and Shared) mobility. This and other underlying trends will have a significant influence on, among others, car, plane, and industrial asset manufacturers, particularly in terms of their future investments and time to market.
I’ve already alluded to the growth and transformation in the automotive industry. For traditional OEMs, the demands of developing new systems to stay relevant and, at the same time, compete with the new giants like Tesla, are huge. Of course, the experience of manufacturing products does play a role. However, the whole development cycle needs to be robust, agile, and cost-effective. The challenges of developing systems, for example, battery technology with reliability, range and robustness needs balancing with the time-to-the-market. The only way to achieve this is by reducing the development cycle via virtual testing and doing early correlation, verification, and validation to increase confidence in the virtual tests.
A typical product development cycle starts with computer-aided engineering, followed by design optimization methods to refine the design according to a certain target. This involves making decisions regarding several factors, including the warranty period of assets, cost targets, and many other targets such as space, weight, power, etc.
With an optimized design in place, simulation, advanced prototyping, and virtual testing methods and capabilities deliver the first results. However, the complexity of hardware and different test scenarios are effort- and cost-drivers for the verification and validation phase of those physical designs.
In the past, OEMs would build their first mock-ups or prototypes at this stage, to measure accurate loads, attain motion data and the resulting damage information for a vehicle. But today’s advances in virtual testing, simulated environments, and prototype environments, allow customers to simulate loads, parametric variations of structures, noise, and many other parameters to validate their ideas in a virtual environment designed to simulate real use scenarios.
Upon completion of the virtual optimization, prototypes are built and tested, using physical testing methods to ensure that the prototype meets the physical design criteria.
And finally, pre-release, the homologation process starts, to ensure that vehicles, for example, meet the requirements of legislation and standards in terms of noise emissions, exhaust emissions, etc., before being released for manufacture and onto the market.
These steps are all part of product design life cycle. Once the product is in the market, it generates a wealth of data and important information during its lifetime. These real-world data sets are important for the next iteration of the product development cycle, creating important information for designers that can help to further improve the next generation of the product. The continuous, open, and interoperable data flow is paradigm of those iterative design processes.
We have been focusing on ways to accelerate and improve the product design life cycle, specifically in terms of reliability and durability.
This type of design optimization is a key opportunity that needs to be explored as the current convergence of classic fatigue testing, classic material science and new techniques such as those used in e-power could be areas where we can shorten the cycle.
Engineers have used computer-aided design tools and methods for over a decade, and it has reached the point where computer-aided simulation has become a standard tool in the first design phase.
Simulators and virtual testing offer OEMs significant potential to acquire information, or to ingest parametric variations early in the development process. For example, gaining insight into how the product will behave in real-life scenarios can shorten the design life cycle significantly.
However, based on feedback from customers, we understand that the trust in virtual models varies based on the complexity of the system and from whole vehicle to components layers. HBK’s main drive is to help customers bridge the gap between the physical and virtual world. We provide actional insight through our advanced instruments and test equipment, augmented by the power of our software and services.
Test automation is also an important area for OEMs. Once a prototype reaches the physical testing stage, it is important to manage complex tests and test scenarios as efficiently as possible. These tests can involve thousands of sensors, and even one sensor failing can result in not only the loss of thousands of hours of testing, but also terabytes of valuable data.
These three key areas – design optimization, simulation/simulators, and test automation in combination with physical competence and domain expertise can create new insights to help OEMs accelerate time to market.
In Part 2 of this interview, Jens will expand on how technology can help shorten product development cycles and the next big breakthroughs for product development teams.
Accelerate your product innovation with HBK solutions in virtual, physical and in-process testing. From the electrification of mobility to the advancement of smart manufacturing, we support you throughout the entire product lifecycle, sharing your mission for a cleaner, healthier, and more productive world.
This will bring together HBM, Brüel & Kjær, nCode, ReliaSoft, and Discom brands, helping you innovate faster for a cleaner, healthier, and more productive world.
This will bring together HBM, Brüel & Kjær, nCode, ReliaSoft, and Discom brands, helping you innovate faster for a cleaner, healthier, and more productive world.
This will bring together HBM, Brüel & Kjær, nCode, ReliaSoft, and Discom brands, helping you innovate faster for a cleaner, healthier, and more productive world.
This will bring together HBM, Brüel & Kjær, nCode, ReliaSoft, and Discom brands, helping you innovate faster for a cleaner, healthier, and more productive world.
This will bring together HBM, Brüel & Kjær, nCode, ReliaSoft, and Discom brands, helping you innovate faster for a cleaner, healthier, and more productive world.