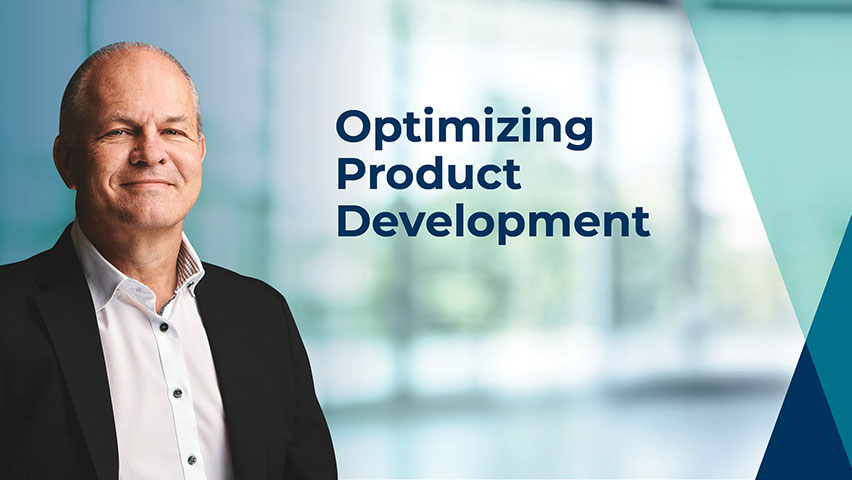
Nowadays, many macro trends, for example, connectivity standards, computational power, and artificial intelligence (AI), enable the acceleration of virtual testing concepts, and experimental prototyping will become more common. The automotive industry is already very experienced and knowledgeable in these areas, but other industries could, should and probably will apply simulation technology and simulated environments more and more in the future.
There are, of course, scenarios where capturing the physics using simulation techniques –particularly multi-physics – remains a challenge. Many active systems, once integrated into the product, are extremely difficult to model using state-of-the-art methods. Here, the trend is more towards iterative prototype testing at the sub-system level than complete system level. This helps engineers to understand the failure modes early in the process.
Over the past 20 years, we have seen significant innovation in these technologies. I used to say that there is more base technology in the market today than we can consume, but these rich environments are now ready for deployment.
In short, simulating systems or sub-systems, using either physical sub-systems on a rig or simulation or computer-aided-engineering tools, will help shorten the development life cycle. To maximize the potential of this digital transformation, virtual modelling and analysis must be aligned with physical test and measurement to generate cleaner and more actionable data.
Yes. The technologies mentioned have not only decreased development costs, but I think they also enable ‘design for X’. I use the term design for X to mean ‘design for cost’, ‘design for quality’, ‘design for warranty,’ and so on – essentially design space optimization.
To return to the example of a modern e-car – the price of the battery often accounts for more than half the car’s production cost. Car owners and leasing companies need to know how long the battery will last.
Reducing development time via design optimization, use of simulation and automated testing will not compromise quality at all – quite the opposite; these technologies improve quality.
The convergence of hardware and software capacities and the use of model-based development will further drive the digital prototyping area. This is an area that HBK is looking to expand into.
The recent COVID-19 pandemic has now become an accelerator, driving a whole range of product development trends and new ways of working. We are now used to working remotely in global teams from our home offices, a situation that also applies to engineers who are designing cars, trains, and other complex products.
This necessary shift in ways of working will accelerate transformation in collaborative tools, leading to the development of more robust remote or virtual environments across the industry. OEMs will continue to face increasingly tough and complex challenges not just during the pandemic.
HBK’s goal is to help them cope with those challenges and accelerate the digital transformation with innovative solutions. We provide customers with expert insight through our advanced instruments and test equipment, augmented by the power of our software and services. This equips customers with the ability to reduce time to market, improve processes, quality and yield. In this way, Spectris know-how creates value for our wider society, as our customers design, develop, test and manufacture their products to make the world a cleaner, healthier and more productive place.
Open systems will become increasingly important to manage the interoperability of the different solutions and data during the design life cycle. This openness will deliver value for HBK customers, allow them to pick the best solution ad the best insights from the sea of data, and support them in taking safer, more energy efficient and more innovative products to market as quickly as possible.
Accelerate your product innovation with HBK solutions in virtual, physical and in-process testing. From the electrification of mobility to the advancement of smart manufacturing, we support you throughout the entire product lifecycle, sharing your mission for a cleaner, healthier, and more productive world.
This will bring together HBM, Brüel & Kjær, nCode, ReliaSoft, and Discom brands, helping you innovate faster for a cleaner, healthier, and more productive world.
This will bring together HBM, Brüel & Kjær, nCode, ReliaSoft, and Discom brands, helping you innovate faster for a cleaner, healthier, and more productive world.
This will bring together HBM, Brüel & Kjær, nCode, ReliaSoft, and Discom brands, helping you innovate faster for a cleaner, healthier, and more productive world.
This will bring together HBM, Brüel & Kjær, nCode, ReliaSoft, and Discom brands, helping you innovate faster for a cleaner, healthier, and more productive world.
This will bring together HBM, Brüel & Kjær, nCode, ReliaSoft, and Discom brands, helping you innovate faster for a cleaner, healthier, and more productive world.
This will bring together HBM, Brüel & Kjær, nCode, ReliaSoft, MicroStrain and Discom brands, helping you innovate faster for a cleaner, healthier, and more productive world.