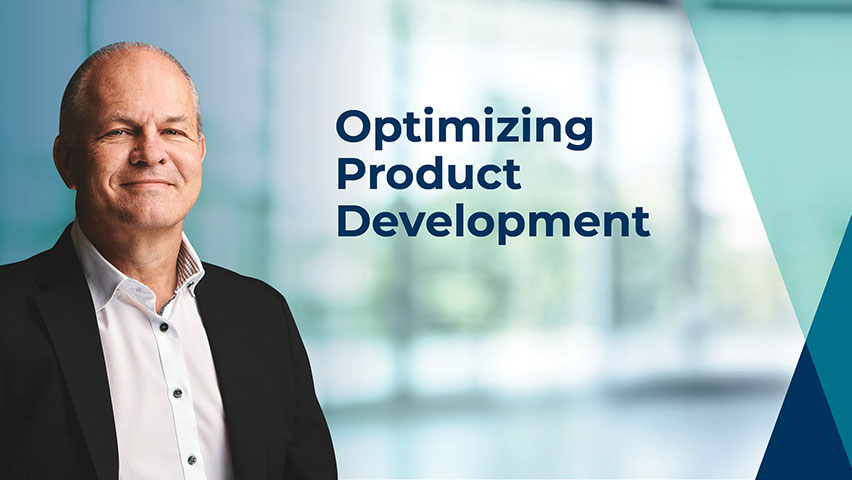
Everything starts with proper preparation. To make everything run smoothly, seek for a clean work space and, collect all the materials you’ll need for the installation ahead of time.
The most important step is to prepare the space where you’re going to mount the strain gauges. First, degrease the area before sanding it using an emery cloth, a hand held sander, or a sandblaster. Be sure to use a new and clean piece of sandpaper or new blasting sand.
Clean the space you have sanded using a surface cleaning agent such as the HBK RMS1 spray, which frees surfaces of dirt, grease, and other impurities. Be sure to use a clean and lint-free pad when wiping down the area.
Once the surface has been prepared, use an empty ballpoint pen for marking out the measuring points. Not only does the pen show strain gauge positioning, it does not produce the sharp burs that occur when using a scriber — which would damage the strain gauge.
Save time by preparing your measuring points in one step, no matter how many strain gauges you plan to install. It’s crucial to protect the sanded and cleaned surface from oxidation until you install the strain gauges. Use only residue-free removable adhesive tape that is silicon-free
We suggest that you only use pre-wired strain gauges so you do not have to perform soldering. This also eliminates the need to remove residual flux from the area.
Select the right adhesive. There are many types of adhesives available to attach your strain gauges. We highly recommend a cold curing adhesive such as HBK’s Z70 product for bonding your strain gauges. Such fixatives are single component adhesives, do not require mixing, and cure quickly. For example, Z70 cures on very slight adhesive films, at room temperature, and under thumb pressure.
Protect strain gauges around their entire surface. Aluminum foil coated with a 3-mm thick kneading compound, such as HBK’s ABM75 accessory, helps to safeguard strain gauges from weather and water.
Connect the strain gauges to an amplifier, such as something similar to the QuantumX MX1615B, because it is possible to connect the strain gauge cables to the amplifier module without soldering.
Select the right analysis software. For those who wish to start measuring immediately from their computer, we recommend software that simplifies the acquisition, visualization, and analysis of your measured data. HBK’s catman software will help you get your results quickly — and easily configure and visualize your next measurement.
Accelerate your product innovation with HBK solutions in virtual, physical and in-process testing. From the electrification of mobility to the advancement of smart manufacturing, we support you throughout the entire product lifecycle, sharing your mission for a cleaner, healthier, and more productive world.
This will bring together HBM, Brüel & Kjær, nCode, ReliaSoft, and Discom brands, helping you innovate faster for a cleaner, healthier, and more productive world.
This will bring together HBM, Brüel & Kjær, nCode, ReliaSoft, and Discom brands, helping you innovate faster for a cleaner, healthier, and more productive world.
This will bring together HBM, Brüel & Kjær, nCode, ReliaSoft, and Discom brands, helping you innovate faster for a cleaner, healthier, and more productive world.
This will bring together HBM, Brüel & Kjær, nCode, ReliaSoft, and Discom brands, helping you innovate faster for a cleaner, healthier, and more productive world.
This will bring together HBM, Brüel & Kjær, nCode, ReliaSoft, and Discom brands, helping you innovate faster for a cleaner, healthier, and more productive world.
This will bring together HBM, Brüel & Kjær, nCode, ReliaSoft, MicroStrain and Discom brands, helping you innovate faster for a cleaner, healthier, and more productive world.