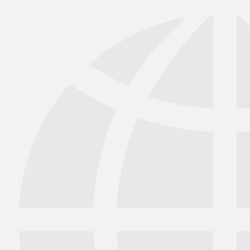
Monitoring of a multitude of process parameters ensures that the system's performance always is adapted to the permanently and sometimes very rapidly varying operating conditions while at the same time maintaining high efficiency. This is a major challenge with mechanical propulsion systems in particular. One of the most important process parameters is the propulsion power transmitted to the gas compressor. It is essential to control its generation in such a way that the minimum propulsion power required for the compressor's particular operating situation is permanently available, even with fast changing loads. At the same time, generating excessive propulsion power results in reduced efficiency and, moreover, in increased pollutant emissions (with mechanical propulsion systems) as well as in critical operating states (in particular with mechanical propulsion systems with gas engines). Permanent monitoring and control of the propulsion power of such systems therefore requires the compulsory measurement of rotational speed and, in addition, measurement of the torque transmitted to the compressor. Contrary to rotational speed measurement that can be implemented directly and relatively easily, implementing torque measurement is rather difficult. For this purpose, measurement quantities such as cylinder pressure and temperature are often used as auxiliary quantities and as the basis for calculating torque and thus power. This method has been used for many years and has been permanently refined; however, it has the disadvantage that the measurement uncertainty related to torque significantly increases due to a number of parameters with higher tolerances used for this purpose and, moreover, usually cannot be convincingly proven. Greater tolerances of measurement quantities required for control purposes, however, inevitably result in larger deviations from the optimal operating parameters. This can have undesirable effects, in particular with the gas engine. This will be illustrated by the following chart:
Operating range of a gas engine Source: Wärtsilä Corporation
It shows the relationship of brake means effective pressure (BMEP) and air/fuel ratio which enables knocking and misfiring areas to be visualized. In no case must the engine's operating point be in one of these areas; in particular, it is essential to make sure that, in all operating conditions, it does not shift to the knocking area, since this can cause damage to the engine. The optimum operating window is the area between knocking and misfiring and gets narrower toward the top. This means that operating the gas engine at maximum power while maintaining low pollutant emissions requires a sensitive control mechanism with small tolerances. Higher tolerances necessarily mean reduced maximum power to increase the distance between the operating point and the knocking and misfiring areas. At the same time, it is essential that the control is very fast, since large pressure fluctuations can occur at the compressor within a small time frame, which become noticeable as load variations at the engine. They need to be quickly and precisely compensated for by the engine to ensure that the operating point remains in the safe operating window. The following chart shows that these load variations can amount to about 50% of the system's capacity within a few seconds:
Load variations of a gas compressor set Source: Wärtsilä Corporation
Installation of a torque flange, i.e. a specially optimized shaft section or adapter into the drive train is an elegant way of directly measuring the torque transmitted to the compressor. This method means that the measurement system is an integral part of the measuring body and thus of the shaft section; both components can only be calibrated together. The torque flange is designed such that it can reliably transmit the maximum torque while at the same time offering high sensitivity. The manufacturer uses a torque calibration machine to calibrate and accordingly certify the torque flange for the required torque. Its design allows easy installation in and removal from both the drive train and a calibration machine. The measurement signal is transmitted from the torque flange rotating with the input shaft to an evaluation unit using a telemetry system; the transducer is fed in the same way vice versa. Using a torque flange provides further advantages in addition to direct and very precise measurement of the torque transmitted to the compressor:
Torque flanges have primarily been used in automotive power test stands over the past decades. Rising energy costs, ever more stringent regulations for emission values and related developments in drive technology have resulted in this technology having been adopted in other industries, for example, in the oil and gas as well as in the marine industry. High operating costs in applications in these fields have also led to torque flanges' increasingly being used for control tasks in addition to their classical field of application in power test stands.
Klaus Weissbrodt HBM Key Account and Project Manager
High-capacity Torque Applications
This will bring together HBM, Brüel & Kjær, nCode, ReliaSoft, and Discom brands, helping you innovate faster for a cleaner, healthier, and more productive world.
This will bring together HBM, Brüel & Kjær, nCode, ReliaSoft, and Discom brands, helping you innovate faster for a cleaner, healthier, and more productive world.
This will bring together HBM, Brüel & Kjær, nCode, ReliaSoft, and Discom brands, helping you innovate faster for a cleaner, healthier, and more productive world.
This will bring together HBM, Brüel & Kjær, nCode, ReliaSoft, and Discom brands, helping you innovate faster for a cleaner, healthier, and more productive world.
This will bring together HBM, Brüel & Kjær, nCode, ReliaSoft, and Discom brands, helping you innovate faster for a cleaner, healthier, and more productive world.
This will bring together HBM, Brüel & Kjær, nCode, ReliaSoft, MicroStrain and Discom brands, helping you innovate faster for a cleaner, healthier, and more productive world.