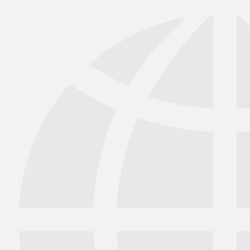
Installing your rotating torque sensor properly is critical for two overarching reasons. The first is to reduce measurement uncertainty, and the second is to reduce the risk of failure.
Improper mechanical installation can prove to be catastrophic for test benches, particularly in high-value applications where advanced measurement systems represent an enormous investment. In this article, HBM will offer a few brief tips on how to correctly install your rotating torque sensor and maintain confidence in your operation.
The first and potentially most important thing to remember is that torque transducers are extremely sensitive devices that must be handled with care. How you do this largely depends on the type of sensor you are integrating into your system. Heavy, large-capacity torque sensors often have threaded holes, for example, which can be used to maneuver the device using eyebolts and straps. Also, it is imperative that all sensors are safely packed with protective media during transit.
The next thing to bear in mind is the design of your driveline, which will dramatically impact both the performance and service length of your test system – alongside the confidence in your readings.
One of the primary concerns with rotating torque sensors specifically is that when you put the sensor in-line you are adding length and weight to the shaft while reducing stiffness. These will result in a critical speed, which means that at certain revolutions per minute (RPM), the shaft is going to become unstable. By keeping the shaft as short as possible and installing the sensor as close to a bearing as possible, you can avoid critical speeds or shift them to higher uncritical regoins. Similarly, it is important to balance your torque sensor to avoid damage from vibration.
There is a set of basic mechanical principles that should be adhered to when designing your driveline and installing your rotating torque sensor, but it is important to remember that different configurations will require different mechanical parameters to reach maximum efficiency. For instance: When measuring peak torque, you are going to want a torsionally rigid coupling capable of transmitting accurate torque information at high RPMs. However, for lower speed torque signals, coupling rigidity can be relaxed.
This also depends upon the type of mounting used – typically either foot-mounted or floating. As mentioned earlier, it is always best to install the torque sensor as close to a bearing as possible to eliminate vibration, particularly for floating drivelines. There are too many possible configurations to cover in a single article, so please refer to our in-depth technical note below for more detail on specific driveline setups:
Installing your torque sensor properly is vital to successful data acquisition. We appreciate that no two systems are alike and that covering the broad strokes of installation here may not answer all of your questions. Yet the HBM team is always happy to help. Contact us today if you have any specific queries about rotating torque sensor installation, or for more information on our transducer range.
This will bring together HBM, Brüel & Kjær, nCode, ReliaSoft, and Discom brands, helping you innovate faster for a cleaner, healthier, and more productive world.
This will bring together HBM, Brüel & Kjær, nCode, ReliaSoft, and Discom brands, helping you innovate faster for a cleaner, healthier, and more productive world.
This will bring together HBM, Brüel & Kjær, nCode, ReliaSoft, and Discom brands, helping you innovate faster for a cleaner, healthier, and more productive world.
This will bring together HBM, Brüel & Kjær, nCode, ReliaSoft, and Discom brands, helping you innovate faster for a cleaner, healthier, and more productive world.
This will bring together HBM, Brüel & Kjær, nCode, ReliaSoft, and Discom brands, helping you innovate faster for a cleaner, healthier, and more productive world.
This will bring together HBM, Brüel & Kjær, nCode, ReliaSoft, MicroStrain and Discom brands, helping you innovate faster for a cleaner, healthier, and more productive world.