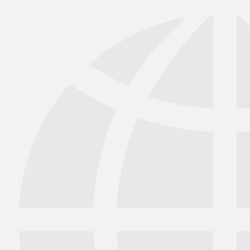
The job of testing mobile power, transient power, in-vehicle power and efficiency has several unique challenges . One is that there is no steady state frequency: vehicle speed is constantly changing - increasing or decreasing. Only very rarely does a driver get in a car and travel at a fixed speed for the entire journey.
There are some issues with the way traditional instruments handle tracking frequency. A lot of the more traditional instruments were originally developed for the grid, so they use a phase lock loop system and require a fixed frequency. That means using them in a vehicle where speed and electrical frequency is constantly changing creates some real challenges in obtaining accurate, reliable measurements.
There are constantly changing states in these electric machines, specifically for road testing. Think of vehicles accelerating from a stoplight and hybrids that are clutching in and out. Transients can occur, such as hitting things or wheels slipping on ice. There are a variety of issues that can come up.
Tracking a machine as it slows down over time is difficult with traditional equipment. HBK combats this issue by using a cycle detect system. Digital algorithms that track zero crossings are used to determine cycles for making power calculations. This allows dynamic testing.
Drive cycles and in-vehicle testing require dynamic power measurements. Dynamic power has a lot of importance.
This first graph – acceleration - shows the scooter accelerating from zero to a certain speed. Current is shown in red, voltage in blue, and then power, reactive power and apparent power in black, pink, and yellow respectively. The kickback needed to start the scooter can be seen. The scooter's inverter then activates and the PWM kicks on. There is a little in-rush and then as that frequency increases and the scooter speeds, the bands can be seen getting tighter. There is a little bit of overshoot and then a more steady state.
Throughout recording, the cycle detect in black can be seen tracking that current all the way. The cycle detect allows measurement of signals as frequency changes. As the current value gets close to zero, the frequency is increasing. Then there are power values that are steadily increasing with vehicle power. There is a little in-rush of current where the scooter was kicked, as power was actually being put into the system. As that power is increasing, there is windage from the hills that are causing real-world oscillation in power as it is increasing. After this, there is an overshoot from the extra power. In these dynamic scenarios, more power is being used up than would normally be used.
This is a valuable tool for understanding how far a vehicle is going to go with an actual driver, an actual powertrain and actual road conditions. Dynamic testing lets users characterize real-world scenarios. It gives an accurate estimate for the range of the vehicle and allows optimization of the powertrain to perform better on EPA driven or governing body driven tests.
The second graph – regeneration - shows deceleration and going into regeneration, which is a particularly fascinating state. The current can be seen reducing in frequency and the PWM decreases in frequency. As speed decreases, power rolls off.
Regeneration affects driver experience and creates additional losses with poor management. Real power, in black, becomes negative as power is put back into the system. At a certain point, whilst slowing down, that power becomes positive again. Energy is actually being wasted operating regeneration. This consumption of energy during regeneration has to do with the losses in the machine due to heat being more than the amount of power being put back into the battery.
This is not only to do with experience but also to do with range and how power flow is managed. There is a lot of very valuable engineering information that can be gained from taking the raw data on a drive cycle and translating it back to how a vehicle can be improved for a given operating state.
The job of testing mobile power, transient power, in-vehicle power and efficiency has several unique challenges. One is that there is no steady state frequency: vehicle speed is constantly changing - increasing or decreasing. This White Paper examines real-world performance analysis of electric machines and ways to manage the challenges of dynamic testing.
These drive cycles depicting real-world scenarios can be taken and replayed on a dynamometer. You can take the equipment from the vehicle, bring it to a test stand, and then replicate the torque-speed combination. The images above show a torque pattern (red) and a speed pattern (blue) for the World Harmonized Light Vehicles Test (WLTC). It is clear that to get given speeds for this drive cycle, a certain torque needs to be applied. In this 30-minute test, as well as torque and speed motor loss was also measured, which showed that the losses from the machine came from different elements. Winding temperatures. Were also measured and lastly, some real time estimations were carried out to get magnet temperature.These are all things that could be done in-vehicle on a chassis dyno, in-vehicle on the road, or on a dyno for R&D purposes. The tests help you to understand where your losses are highest so you can start to minimize them.
A lot of the time, especially when we are looking at transient states, it is important to understand how a controller handles the situation. Does the controller behave acceptably during transients? Getting an understanding of what the machine controller may be doing is useful for calibration and for reverse engineering or benchmarking. Understanding calibration is important for customer experience.
The jump scenario was plotted in the space vector plane (shown above) to form an idea of how the controller was handling this given transient situation.
The first graph shows that there is a high fundamental frequency of low torque and that then a lot of current and torque is applied when the vehicle lands. Flux in the magnetization can then be seen.
The brown area in the initial graph is then plotted in a stationary frame DQ0. The system goes from operating in the center, to the current applying itself and gaining traction with the machine, eventually giving rise to the circular pattern. This information has a lot of power in terms of tuning and understanding how to optimize the controller.