Rugged Data Acquisition Systems for Field Tests of Off-road Vehicles
Just as engineers of consumer vehicles are being asked to shorten development cycles and improve performance, reliability, and safety, so are developers of off-road vehicles, such as construction vehicles and agricultural machinery. From a practical point of view, this means running more tests and acquiring and analyzing more data in a shorter time than ever before. Good measurement data is, after all, important for optimizing designs.
Consider the following types of vehicles:
- A tractor plowing the dusty expanses of a Kansas wheat field, powering through the mud in blistering heat.
- A crane at a skyscraper building site, conveying tons of materials up several hundred meters high.
- A ship carrying needed supplies to offshore oil rigs that must get through no matter how bad the weather.
- A truck transporting material carrying tons of recently-mined ore.
Each of these scenarios share some common measurement requirements. The data acquisition system,
SomatXR, used to test these vehicles must be rugged enough to withstand field testing, provide accurate and repeatable measurements, and be able to acquire data over the Web.
In addition, however, each scenario has its own unique requirements. That being the case, the flexibility to adapt to different measurement tasks is a very desirable feature for data acquisition systems used to test off-road vehicles.
To make optimum use of time while testing a prototype, it is important for the measurement system to be able to withstand all kinds of harsh conditions. Rugged data acquisition systems are needed for testing in harsh environments to reduce test times and keep the cost of repairs as low as possible.
Testing off-road vehicles presents many challenges. Perhaps the most challenging is the operating temperature range. Some vehicles must operate at temperatures as low as -30°C, if, for example, they will be used in northern climes during the winter, while others may have to operate at temperatures up to +80 °C, if they are to be used in the desert during the summer.
For performing winter tests, such as cold-cranking tests, and summer tests, such as cooling tests, you'll need a data acquisition system that can operate at very low temperatures and very high temperatures. A data acquisition test with an extended operating temperature range doesn't need any special packaging to operate under these extreme temperature conditions.
Shock and vibration is also a consideration for testing vehicles that must operate on off-the-beaten-track and unpaved roads. To help ensure that your data acquisition system will operate reliably in an environment with harsh vibration and sudden impacts, look for equipment that has been tested using test procedures found in MIL-STD-202G, “Test Method Standard: Electronic and Electrical Component Parts.” This standard specifies environmental tests used to test military electronic gear, including shock and vibration testing. Look for a MIL-STD-202G vibration rating of 10 g and a shock rating of 75 g.
Dusty and wet conditions are common when testing agricultural and mining vehicles. To ensure that your test equipment will operate in conditions that are dusty or wet, look for equipment that has an IP65/67 rating. IP ratings, or ingress protection ratings, specify how well the enclosures protect against dust and water. IP65 enclosures are dust-proof and protect against water jets. IP67 enclosures are dust-proof and immersible in water up to a depth of 1 m.
IP ratings were developed by the IEC (International Electrotechnical Commission) and are mostly used in Europe, but there are NEMA equivalents. An IP65 rating corresponds to a NEMA 4 or 4X rating. An IP67 rating corresponds to a NEMA 6 or 6P rating.
Protect against unforeseen events
When operating under such extreme conditions, it's hard to anticipate all of the problems that may occur. Nothing is more aggravating than losing measurement data because of unforeseen events, such as a power failure or the data acquisition program crashing. This is especially true for long-term tests, when the user is not always on site to monitor error-free recording of measurement data.
For situations like this, a measurement system that records data as it goes, and can pick up where it left off, is indispensable. Should there be a power outage, or some type of vehicle failure that interrupts a test, you at least have whatever data has been recorded up to that time. The system should also continue data logging automatically after the interruption without any need for user interaction.
Another way to protect against unplanned interruptions is to check to see that the system you purchase uses a stable operating system. It has been our experience that using a Linux operating system provides the most stability for applications such as these.
Web-based measurements makes life easier for test engineers
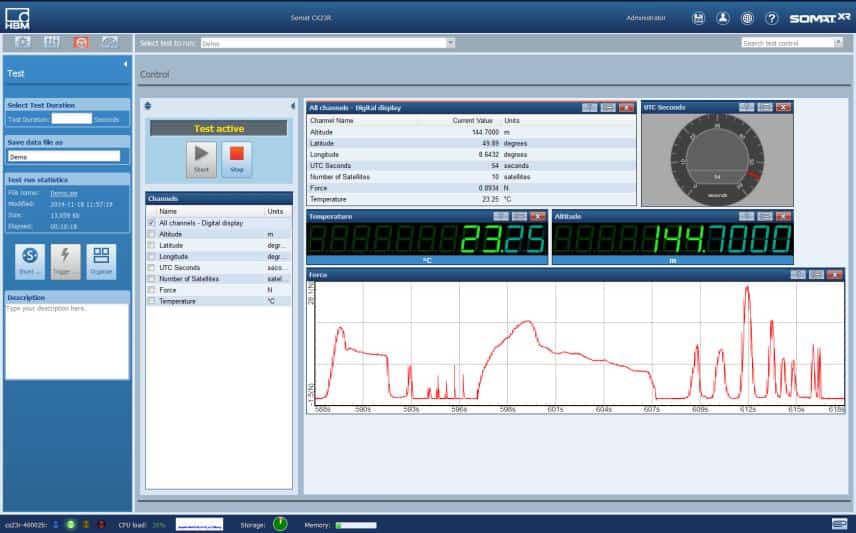
The ability to access a measurement system via the Web is very convenient when testing in harsh environments and when performing long-term tests. If your measurement system has a Web interface, you can monitor the test remotely and not have to monitor it on site.
Typically a Web interface provides direct access to the measurement data – anywhere, from any web-capable device. With the right software, you can visualize test results in real time, too. In addition, a Web interface can allow multiple clients to access the system and focus on the test data that is important for them.
In addition to acquiring test data remotely from your office, a data acquisition system used for testing off-road vehicles should allow you to modify a test setup. This feature allows you to make changes in hours instead of the days that may be required to fly a test engineer or technician to a remote test location.
Modular architectures offer the ultimate flexibility
Because off-road vehicles come in so many different sizes and shapes, and the measurement requirements are so diverse, your data acquisition system needs to be very flexible. Systems with a distributed modular architecture make it possible to structure the system according to these varying requirements, thereby reducing overhead.
For example, when testing a very large system, such as a construction crane, your system should allow you to position a data acquisition module close to where the measurements need to be made. Positioning the module close to the measurement point will minimize the effect of long sensor leads and common-mode noise, which can cause measurement errors.
Another feature that can improve the flexibility of a data acquisition system is universal inputs. Modules with universal inputs allow you to connect different types of sensors to a data acquisition module and record different types of parameters with a single module. This reduces the number of modules that you'll need for a particular test.
Finally, consider how the software functionality of your data acquisition system makes the system more flexible. One feature that you might look for is intelligent processing of channel data. It is, for example, very convenient to perform real-time calculations on acquired data and then record the calculated values as an independent channel or trigger measurements using the calculated data.
One of these flexible systems is the SomatXR solution from HBM. All aspects of its hardware and software are designed to be rugged to ensure maximum data security. The distributed modular system is much more flexible than a stackable modular design. It also offers additional functions for intelligent processing of channels, such as calculated channels, triggers and data manipulation.
Testing off-road vehicles is definitely challenging. Modern data acquisition systems are up to the challenge though. They offer reliable and robust measurement capability that you can use in all kinds of adverse conditions, and that makes your job a little easier.