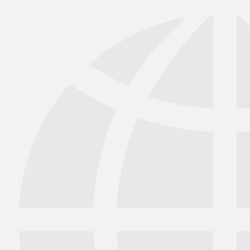
Condition Monitoring Systems (CMS) are designed to ensure the long-term<strong> efficiency of wind power plants. In the future they will also monitor important components such as rotor blades, towers and foundations. The focus moves here to optical sensor technology as an alternative to electrical technology.
Structural and condition monitoring on edifices such as bridges and buildings has been the subject of research and development for a long time already. HBK has been a specialist in Experimental Stress Analysis for more than 6 decades, providing precisely matched solutions for this task along the entire measuring chain. Numerous results of examinations have already been published in this area. [1], [2], [3]
[1] Henke, V. "Monitoring the Reichenbach and Albrechtsgraben viaducts"; RAM; Reports in applied measurement, No. 1/2007; pages 10-20, Darmstadt, 2007
[2] Liebig, J. P.; Menze, O.: "Keeping an eye on the effects of heavy goods traffic: long-term monitoring of a prestressed concrete bridge," HBM application report 10/2009, Darmstadt, 2009
[3] Gommola, G.; "Are our bridges safe? bridge monitoring with measurement technology from HBM," pp. 22-23; HBM customer magazine "hotline" issue 1/2012
[4] Germanischer Lloyd: Guideline for the Certification of Offshore Wind Turbines, 2005
[5] Steingröver, K.; et al. "Condition Monitoring Systems for Wind Turbines: Current status and outlook on future developments from the perspective of certification"; VDI report on "Vibrations in wind turbines," Bremen, 2010
[6] Steingröver, K.; et al. "CMS für Windenergieanlagen aus Sicht der Zertifizierer" [CMS for wind energy systems from the point of view of the certifier] "ECONOMIC ENGINEERING" Journal, issue 5/2012, Göller Publishing house, Baden-Baden
[7] Frieling, G.; Walther, F.: Tensile and fatigue properties of Fiber-Bragg-Grating (FBG) Sensors. In: Sensors & Transducers Journal 154 (2013), No. 7, p. 143-148
[8] Zerbst, S.; Knops, M.; Haase, K.-H.; Rolfes, R.: "Schadensfrüherkennung an Rotorblättern von Windkraftanlagen" [Early detection of damage on rotor blades of wind power plants], Lightweight Design issue 2010-04, Vieweg +Teubner, Wiesbaden
[9] Haase, K.-H.: Underwater application of strain gauges, UK Environmental, 2004.
[10] HBM/HBK Website, 2014. OptiMet by HBM
(jv)
* Dr. Karl-Heinz Haase, Product and Application Manager Optical Technology & Asset Monitoring; Dr. André Schäfer, Product and Application Manager Calibration/Wind Energy; Hottinger Baldwin Messtechnik GmbH
This will bring together HBM, Brüel & Kjær, nCode, ReliaSoft, and Discom brands, helping you innovate faster for a cleaner, healthier, and more productive world.
This will bring together HBM, Brüel & Kjær, nCode, ReliaSoft, and Discom brands, helping you innovate faster for a cleaner, healthier, and more productive world.
This will bring together HBM, Brüel & Kjær, nCode, ReliaSoft, and Discom brands, helping you innovate faster for a cleaner, healthier, and more productive world.
This will bring together HBM, Brüel & Kjær, nCode, ReliaSoft, and Discom brands, helping you innovate faster for a cleaner, healthier, and more productive world.
This will bring together HBM, Brüel & Kjær, nCode, ReliaSoft, and Discom brands, helping you innovate faster for a cleaner, healthier, and more productive world.
This will bring together HBM, Brüel & Kjær, nCode, ReliaSoft, MicroStrain and Discom brands, helping you innovate faster for a cleaner, healthier, and more productive world.