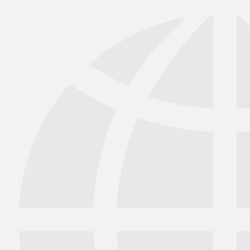
The torque signal in tests of combustion engines exhibits dynamic behavior. The reason for this is vibrations and oscillations caused by the working cycles of each individual cylinder. These dynamic, periodically oscillating torque components are superimposed over the actual torque measurement. The CASMA filter (Crank Angle Sampled Moving Average) works in angular synchronism and is time independent, thus allowing to automatically respond to RPM changes. This filter does not work in the time domain. Instead it works synchronously to the angle. In this article you will learn how to apply the CASMA filter in HBM's TIM-PN, TIM-EC and PMX signal conditioning systems.
Parameterization characteristic | Function |
Angle divider | Reduces the angle resolution, thus allowing higher rotational speeds in the same window width |
Angle range (degrees) | Angle range (window width) over which the moving average operates |
Pseudo speed (rpm) | After the rpm speed, pseudo pulses or a pseudo speed are generated. Otherwise the filter would stop working and the measured value would freeze. |
Information area feature | Function |
Maximum rotational speed (rpm) | The angle pulses/s must be less than the sampling rate of the torque measurement. Otherwise the average would be formed via the same measured value. |
Pulses per revolution | Comes from the number of increments, and the analysis. With active quadrature analysis, the angular resolution is quadrupled |
Angular resolution in degrees | Calculated from the number of pulses per revolution and the divider |
Number of averaged values | Computes the number of measured values used to form the moving average |
This will bring together HBM, Brüel & Kjær, nCode, ReliaSoft, and Discom brands, helping you innovate faster for a cleaner, healthier, and more productive world.
This will bring together HBM, Brüel & Kjær, nCode, ReliaSoft, and Discom brands, helping you innovate faster for a cleaner, healthier, and more productive world.
This will bring together HBM, Brüel & Kjær, nCode, ReliaSoft, and Discom brands, helping you innovate faster for a cleaner, healthier, and more productive world.
This will bring together HBM, Brüel & Kjær, nCode, ReliaSoft, and Discom brands, helping you innovate faster for a cleaner, healthier, and more productive world.
This will bring together HBM, Brüel & Kjær, nCode, ReliaSoft, and Discom brands, helping you innovate faster for a cleaner, healthier, and more productive world.
This will bring together HBM, Brüel & Kjær, nCode, ReliaSoft, MicroStrain and Discom brands, helping you innovate faster for a cleaner, healthier, and more productive world.