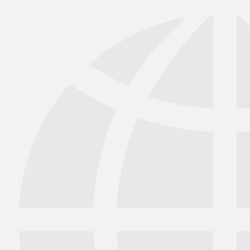
See how HBK's electric motor testing solution system makes accurate testing easier and gathers actionable data to help H3X show the power of its groundbreaking technology for electric aviation.
Gather accurate, actionable data to help H3X show the power of its groundbreaking technology and inform the development of new, boundary-pushing electric motors with integrated inverters.
An accurate, flexible, easy-setup electric motor and drive testing solution comprising of a power and torque measurement system, known as eDrive, plus advice and support from the HBK team.
The H3X team have a richer, more accurate understanding of their products’ capabilities – and easy access to the data they need to show their technology has what it takes to transform the electric aviation industry and beyond.
H3X manufactures the world's most power-dense integrated motor drives (IMDs) ranging from 30kW to 30MW for electric aviation, defense, marine, and heavy industry.
H3X is changing the face of aviation, developing some of the most advanced electric motors in the world.
Its innovations promise to make sustainable aviation a reality, removing one of the main barriers to widespread commercialisation of electric aircraft: the combined power density of electric propulsion system technology.
Previously, even the best motors and inverters on the market had a combined power density of 3-4 kW/kg – but estimates suggest that a Boeing 737, for example, would need a propulsion system that can deliver at least 12 kW/kg continuously.
H3X’s ultra-high power density integrated motor drives combine an electric motor, inverter, and (in some cases) a gearbox into a single unit – the perfect lightweight solution for everything from eVTOLs and drones all the way through to regional aircraft, specialized industrial equipment, and high-speed ferries.
Crucially, H3X’s HPDM family of integrated motor drives offer up to 12 kW/kg continuous power density, making it three times better than current systems – while being efficient and compact enough to reliably power commercial electric aircraft.
In other words, H3X has overcome one of the industry’s most complex challenges – and potentially unlocked a new age of deep decarbonization across aviation, marine, and heavy industrial applications.
But H3X knew that in order to drive widespread adoption – and inform the next phase of product development – the company would need to dig even deeper into its product performance data.
H3X’s products are exceeding the capabilities of even best-in-class motors and inverters, providing significantly more power at a lower weight.
But anyone attempting to revolutionize an industry needs to be able to substantiate their claims – and find ways to continue fine-tuning and improving their products. Not to mention that H3X has needed to complete a wide range of pre-certification tests to ensure that its products are safe, compliant, and ready to go to market.
That’s why accurate, actionable electric power testing data is such an essential part of H3X’s product development process.
Many members of the H3X team had been relying on HBK sensors since their time together at the University of Wisconsin, Madison. So when they needed to upgrade their measurement systems, they knew that HBK sensors could provide the accuracy and ease of testing that they needed.
As James Swanke, H3X’s Senior Motor Design Engineer, said: “I don’t think there are many people that can compete in terms of the accuracies that [HBK] claims.”
When H3X called us for support, we knew exactly what the company needed.
We began by providing H3X with two forms of electric power testing support:
HBK’s Perception software is designed for rapid and reliable processing of large amounts of data, making it an ideal solution for H3X’s fast-paced testing and development.
Having a centralized and synchronized data acquisition platform has allowed the H3X team to identify bugs in its firmware and deliver high-confidence efficiency reports – making it much easier to deliver products that reach the highest possible standards.
The team has also automated much of their test logging for end-of-line and efficiency mapping type tests, and has found that Perception fits smoothly and easily into this process.
This “lowers the stress and data acquisition related workload on test engineers”, says James Swanke.
The maximum thermally-continuous torque on H3X’s HPDM-250, HPDM-30, and HPDM-1500 high-performance motors is a significant selling point – which makes accurate, efficient torque measurement a crucial part of the R&D process.
HBK’s torque sensors provide H3X with the high-precision data the team needs to refine their products and prove that their specs are accurate.
To conduct these measurements, HBK’s eDrive systems were integrated with a dynamometer in H3X’s lab. This dynamometer attaches directly to an H3X HPDM motor and a Genesis mainframe for data acquisition.
The eDrive measurement systems have given the H3X team access to data that they can truly rely on for R&D and product performance testing.
“We’re learning more about our product,” said James Swanke. “And I think being able to have accurate and reliable data acquisition really makes it easier to feed [those insights] back into our engineering process.
“Our models are very sophisticated, but you can’t capture everything.”
Torque and eDrive measurement tests are only a few components of a broad suite of tests that H3X runs as part of its product development process. The team has found that HBK sensors can also be used in a wide range of other testing processes, from accelerometer and phase current measurements to characterizing DC power draw to improve system efficiency and power quality. The H3X team have found it easy to adjust the parameters of HBK’s sensors to suit a wide range of needs and applications – and this flexibility has made overall testing significantly easier.
Throughout testing, the H3X team have found their HBK systems to be easy to set up and intuitive to use, with minimal input needed from the HBK team. But that doesn’t mean they need to do everything on their own: “Whenever we run into things that we’re not familiar with, the tech support is just an email or a phone call away – and within a day they typically get us what we need in order to accomplish what we want,” said James Swanke.
This rapid response and expert support have made the testing and measurement process even smoother.
Whenever we run into things that we’re not familiar with, the tech support is just an email or a phone call away – and within a day they typically get us what we need in order to accomplish what we want.
HBK technology has become an integral part of testing and measurement at H3X, giving the team a deeper, richer, and more accurate understanding of each product’s performance.
And our sensors are likely to continue playing a role in the company’s future.
As a start-up, H3X was focused on proving the power of its technology. But now the company is entering a new era.
It’s now looking to scale up and add new products; of course, new products mean more testing, and a greater need to iron out small inefficiencies.
H3X expects that HBK will be a long-term partner on this journey and continue to play a key role.
Thanks to ongoing communications from its support team, H3X is already aware of some exciting new technology in HBK’s product pipeline that it believes will further improve its processes and reduce switching-related noise during data acquisition of inverter output voltages.
And James expects H3X will continue unlocking new capabilities in its existing HBK systems too: “We seem to learn new features about HBK every time we ask,” he says. “So in the future we’ll be focusing on taking advantage of the full capability of the systems so we can become more efficient when we do intensive long duration tests.”