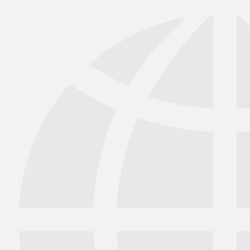
A special universal hydraulic test bench was custom-built, initiated by the wishes of the hydraulic system supplier HANSA-FLEX, conceived by the International Hydraulic Academy (IHA), designed and built by adt-Rinck, equipped with secondary controlled drives from Bosch Rexroth and modern measurement technology from HBK.This test bench can examine complete hydraulic systems with different configurations instead of individual components. In close cooperation with the IHA, adt-Rinck acted as the general contractor and supplied the complete test bench turn-key. This joint project is now set up and working successfully in the R&D department of the IHA in Dresden-Weixdorf.
Until now, hydraulic test benches were designed for special tasks or products. Although the individual components are already tested, the interaction between individual pumps and control systems can only be tested in the machine of the user.
A new universal test bench for hydraulic drives will change all this: This test bench also tests the complex interaction of the individual components. The complete measurement chain from HBK, including the QuantumX amplifier, guarantees safe and reliable results.
This test bench can examine complete hydraulic systems with different configurations instead of individual components. In close cooperation with the IHA, adt-Rinck acted as the general contractor and supplied the complete test bench turn-key. This joint project is now set up and working successfully in the R&D department of the IHA in Dresden-Weixdorf.
The adt-Rinck GmbH is an innovative company in the sector of special purpose engineering, bringing automation and information technology (IT) closer together. The company, founded in 1999, develops and produces industrial data-intensive automation systems. The individual products such as test benches, software controllers, comparison or diagnostic systems bridge the gap between classic automation and modern IT worlds, acquiring, storing and processing process and production data (for instance, in the mass production of hydraulic components or in the automotive industry). Specially developed hardware and software solutions for the evaluation and administration of technical and logistical data supplement or replace commercially available systems.
The test bench consists of an electrohydraulic drive system and the test rig. On the drive side, a total of three secondary-controlled drive systems from Bosch Rexroth operate with speed/torque control electronics (HNC100-SEK with CAN bus connection).
These highly dynamic axial piston pumps work on a common, closed hydraulic pressure circuit with separate hydraulic oil tank. An auxiliary pump from ATOS and the test specimens on the four test desks in total are supplied by a second hydraulic oil tank. The complex hydraulic system with control cabinets, PLC, frequency converter, oil-air cooling system and various measurement technology components is completely controlled by adt-Rinck’s proprietary and customer-specific test bench software.
The operator can run the test bench software close to the test specimen behind a mobile operator protection shield or from the separate control room.
With this universal test bench, the R&D department at the IHA is able to provide manufacturers and operators of hydraulic systems an innovation for their own highly-dynamic tests of pumps in open or closed circuits, hydraulic components and hydraulic manifolds and controls (Test bench characteristics: Power up to 160 kW, max. shaft speeds 2200 or 3200 rpm, torque up to 750 Nm).
The loading energy is redirected by the secondary control system. Instead of converting the entire drive energy with the loading into heat through a pressure valve, up to 60% of the loading energy can be returned. Only the pressure and efficiency losses are lost as heat. The result is a universally deployable system test bench which also boasts a good energy balance.
Hydraulic components, pumps in open or closed circuit and control manifolds can be tested on the test bench. Even four-quadrant operation is possible with the secondary controlled drives, which means that engines for automotive drives can also be emulated.
If a vehicle drives forwards and upwards a positive load is produced, driving downwards produces a negative load. The same applies to reverse travel. These four load cases correspond to the four quadrants. These load cases can be set with individual drive programs on the test bench and then run dynamically. It is even possible to simulate the speed-torque characteristics of diesel engines.
The total efficiency is the sum of the mechanical and hydraulic efficiency.
Mechanical losses result from friction, the hydraulic losses are leak and throttling losses. The losses in a hydraulic system are dependent on the flow rate and pressure losses.
The volumetric efficiency can be determined by measuring the external leaks. Internal leaks can be found by measuring the actual delivery rate of a pump. The external leaks and the actual delivery rate are subtracted from the geometric (theoretical) delivery rate for this.
The individual resistances can be determined by measuring the pressures at different points of the system. If the flow rate is known, the local power loss can be calculated. The largest losses result in hydraulic systems from throttling of the volume flow to control the load speed.
Suitable measurement technology is fundamental to track the losses in the test setup. The mechanical driving power on the pump shaft is measured and compared with the hydraulic power for this purpose.
By approximation the drive power is the product of torque and speed at the pump shaft, hydraulic power is based on volume flow and pressure.
The mechanical input power at the pump shaft is determined by measuring of the torque and speed. The T40 torque flange from HBK is permanently installed on the driveshaft of the pump, the speed is taken from the CAN signal of the HNC100-SEK.
"With regards to our application with the highly dynamic secondary units, it is optimal that each of the two universal HBK Quantum MX840 amplifiers also provide a CAN port. With digital and therefore loss-free mirroring of the CAN signals directly from the HNC to the industrial PC, we can also provide crucial and highly dynamic parameters such as speed, torque, swivel angle for meaningful measurement results via Ethernet to a measurement technology laptop", explained project leader Torsten Sigmund at adt-Rinck. The software was specially developed for this test bench by adt-Rinck.
Each MX840 provides a total of eight input channels for a wide variety of signal transducers. In addition to recording volume flows and torque, the operator IHA measures pressures according to requirements at various points with the HBK absolute pressure transducers types P8AP and P3ICP.
adt-Rinck has been using HBK pressure transducers for years in hydraulic test benches. The entire measurement chain at the test bench consists of the sensors, the two universal and mobile MX840 amplifiers, the intuitive software catman®Easy and a laptop for displaying the measured values in real time, as well as saving and evaluating the data. adt-Rinck adapts the complete measurement technology on the test bench.
Torsten Sigmund gave the reasons for using the HBK software catman®Easy and EasyMath module: "The HBK software offers simple acquisition, very powerful visualization and analysis of measurement data, and is is easy and intuitive to operate".
The test bench is twelve meters long, measured from the reactive power compensation cabinet to the oil-air cooling system, four and a half meters high and six and a half meters wide.
It weights about 25 tons and contains more than 3000 liters of hydraulic oil in two oil tanks. A mobile person protection shield with 10 mm Makrolon panels, developed by adt-Rinck, protects the operator in the event that metal parts or a sharp spray of oil shoot out during prototype tests. Very high pressures up to 400 bar are used in operation here and the hydraulic drives accelerate the shafts from 0 to 2000 rpm in less than 100 ms.
Customers without their own test facilities can now benefit from IHA’s test bench in Dresden to examine their components and systems. The test bench and the measurement system will then be customised individually. The precise test sequence will be defined with the online measurements and then the defined measurements are implemented.
The easy to use calculation channels of the MX840 have proven themselves to be particularly useful according to Dierk Peitsmeyer, head of the IHA R&D department. The experiences gained so far with the novel universal test bench are very good. It delivers repeatable results, IHA’s custom software and the specific functions are running stably. Nevertheless, new ideas are continuously being integrated and the test bench is constantly being developed further by the IHA.
Where necessary, measurements can also be performed on site directly at the customer’s systems because, in contrast to the test bench, the relevant measurement technology is mobile.
The very compact MX840 measurement boxes are withdrawable from the test bench and thereby the measurement software and laptop can be easily taken from the IHA to the customer. These are ideal prerequisites for mobile use. Whatever the mounting position, the small and handy P8AP and P3ICP transducers can be used even when space is limited tight. The pressure measurement results can be rapidly transferred via Ethernet and evaluated on the laptop.
We have been using HBK measurement technology in our national and international test benches forover 10 years and have always had the best experiences with it. The technical properties of the products, their reliability and quality convinced us. We place great value on reliability, accuracy, high signal quality, versatility, comfortable and powerful data logging software. In addition to special product characteristics, advice and services are also important to us. We provide turn-key-solutions and for this the complete HBK package is a perfect fit. It is often an expresswish of our end customers that HBK measurement technology is used in our projects.
This will bring together HBM, Brüel & Kjær, nCode, ReliaSoft, and Discom brands, helping you innovate faster for a cleaner, healthier, and more productive world.
This will bring together HBM, Brüel & Kjær, nCode, ReliaSoft, and Discom brands, helping you innovate faster for a cleaner, healthier, and more productive world.
This will bring together HBM, Brüel & Kjær, nCode, ReliaSoft, and Discom brands, helping you innovate faster for a cleaner, healthier, and more productive world.
This will bring together HBM, Brüel & Kjær, nCode, ReliaSoft, and Discom brands, helping you innovate faster for a cleaner, healthier, and more productive world.
This will bring together HBM, Brüel & Kjær, nCode, ReliaSoft, and Discom brands, helping you innovate faster for a cleaner, healthier, and more productive world.
This will bring together HBM, Brüel & Kjær, nCode, ReliaSoft, MicroStrain and Discom brands, helping you innovate faster for a cleaner, healthier, and more productive world.