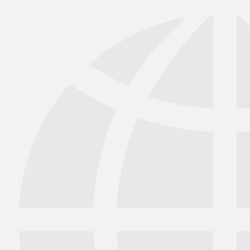
Offshore wind farming is a power generation method that make the best possible use of Japan's long coastline, and in recent years, initiatives are underway to harness wind power in a cost-effective manner (1). Power generated by an offshore wind farm must be transported to land efficiently and inexpensively. The use of a Solid State Transformer (SST) has been recommended, considering that smaller and lighter transformer equipment is necessary to keep costs low. Using a Modular Multi-Level Converter (MMC) could prove especially beneficial, since it is highly efficient, able to be mass produced at low cost, and is flexible enough to handle capacity increases (2). In this paper, we first describe the MMC being researched and developed at the Osaka Institute of Technology, and then show an example of its use in an experiment that was measured with the HBK/GEN series.
Power generated by an offshore wind farm must be transported to land, and it is well-known that costs for transporting power over long distances can be reduced by using DC power transmission instead of AC power transmission.
Fig. 1 shows the DC power transmission system layout of a conventional offshore wind farm (2). The power generator output is boosted and isolated using a 50 or 60 Hz commercial transformer and is then converted to DC by the converter. This configuration poses a problem, because the inductors and capacitors inside the transformer and converter are heavy and have high capacities.
One way to make transformers and inductors smaller is by increasing the frequency of the transformer.
Doing this will allow the size of the magnetic material to be reduced. Setting the frequency to 10 kHz will enable approximately 1/10 capacity reduction (2).
Fig. 2 is a schematic of a DC power transmission system employing a high frequency transformer (2).
The conversion system that employs a high frequency transformer as in Fig. 2 is called a Solid State Transformer or SST. Once the SST has converted the generator output to direct current, it converts it to a high frequency alternating current.
The AC current is then boosted and isolated by a high frequency transformer and then converted back to DC.
The SST contains more transformers than a conventional commercial transformer.However, the capacity and weight of the entire SST can be made smaller. It does, however, perform a greater number of conversions, which means its efficiency is lower. Consequently, the efficiency of the converter needs to be improved.
Using a low-loss switching device is one way to improve the efficiency of the converter. However, since offshore wind farms handle 250 kV to 500 kV in direct current, a high voltage class device like a thyristor must be used for the general converter. The drawback of the thyristor, though, is that it entails large losses.
Another disadvantage is its slow switching speed, which makes it difficult to attain high frequencies.
Utilizing an MMC is an effective way to overcome these issues. Fig. 3 is a circuit diagram of the MMC.
The MMC is comprised of several modules. The switching device used in each module supports low voltages and can handle high voltages in multiple steps. By using the MMC, therefore, we can expect the SST to be highly efficient.
Moreover, when the MMC has a high capacity, it is easily scalable by increasing the number of modules, and if the module is mass produced, its cost can be reduced. Fig.3 shows the circuit configuration used for AC/DC conversion.
In addition, the MMC can perform bidirectional power conversions, so that it may be used as a DC/AC converter.
Fig. 4 shows the circuit diagrams of the module. Adopting a half bridge circuit in the module enables the number of devices to be minimized. However, the module cannot output a negative voltage. Conversely, with a full bridge circuit MMC the number of devices can be increased, and negative voltages can be output by the module allowing it, in turn, to control voltages better than the half bridge circuit MMC, and to exert control over a wider range than the half bridge circuit MMC.
Fig. 5 shows the MMC developed by the Osaka Institute of Technology. It is comprised of a total of 24 modules, 8 modules for each phase. Two module circuits are mounted on each module circuit board. It has a capacity of 10 kVA, and the PWM carrier frequency is 20 kHz or less.
Fig. 6 shows the system configuration used during the experiment. 400 VDC is generated through a rectifier connected to a three-phase system. Then it is converted to three phase 200 V/400 Hz by a two-level inverter, after which it is isolated by a high frequency transformer, and then input to the MMC. The operation of the MMC is then evaluated, as it converts to 400 VDC. Furthermore, as the output of the MMC is input directly to the 2-level inverter, only the power loss of the converter is supplied from the three-phase system.
Fig. 7 shows the setup for the experiment. To analyze the MMC operation, we had to monitor a total of 12 channels simultaneously, including the capacitor voltage of the module, and the currents and voltages of the switching devices. A typical oscilloscope does not have enough channels, so we used a high speed GEN7tA multichannel recorder. Also, the GEN7tA has a sampling of 2 MS/s, and so we were able to measure superharmonics. Moreover, we were able to measure the power of the MMC simultaneously by using the eDrive dynamic power analyze function.
Fig. 8 shows an example of the measurement results of the capacitor voltages for each module. The result clearly shows that the capacitor voltages fluctuate due to MMC operation. The reference potentials of the capacitor voltages are different for each module. Therefore, if a typical oscilloscope is used, we would need a differential probe for each measurement point, whereas with the GEN7tA, the voltage input part is isolated (max. input voltage: ±1000 V), so that it is possible to measure the voltage at many points without the use of differential probes.
The MMC connects several modules in multiple steps. Therefore, to evaluate the MMC we had to measure many voltages and currents. The GEN7tA allowed measurement of up to 42 channels, and to make a detailed operational analysis of the MMC. In future experiments, the Osaka Institute of Technology plans to use the GEN7tA to measure efficiency and switching waveforms.
Osaka Institute of Technology is a private technical university located in Osaka, Japan. It was founded in 1922 and aims to "Develop specialists with science-based practical skills who play an important role in society." OIT offers different undergraduate, graduate and post-graduate degrees in the fields of engineering, robotics and design, information science and technology, as well as intellectual property. Project-based practical learning, like this offshore wind farming system as an example for sustainable and efficient power generation, is what distinguishes Osaka Institute of Technology from other universities.
This will bring together HBM, Brüel & Kjær, nCode, ReliaSoft, and Discom brands, helping you innovate faster for a cleaner, healthier, and more productive world.
This will bring together HBM, Brüel & Kjær, nCode, ReliaSoft, and Discom brands, helping you innovate faster for a cleaner, healthier, and more productive world.
This will bring together HBM, Brüel & Kjær, nCode, ReliaSoft, and Discom brands, helping you innovate faster for a cleaner, healthier, and more productive world.
This will bring together HBM, Brüel & Kjær, nCode, ReliaSoft, and Discom brands, helping you innovate faster for a cleaner, healthier, and more productive world.
This will bring together HBM, Brüel & Kjær, nCode, ReliaSoft, and Discom brands, helping you innovate faster for a cleaner, healthier, and more productive world.
This will bring together HBM, Brüel & Kjær, nCode, ReliaSoft, MicroStrain and Discom brands, helping you innovate faster for a cleaner, healthier, and more productive world.