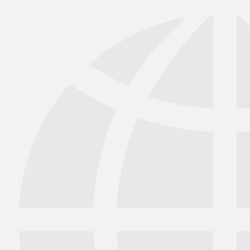
In challenging mechanical and thermal environments that require very high torque, the specialized T40HS torque sensor allows for precise measurement of 1000Nm torque with 0.05% accuracy. If there is any project that deserves to be called "innovative", it is the one recently completed by BCSA and HBK. BCSA specializes in mechanical force introduction systems for sophisticated applications with regard to torque, rotational speed, precision, resilience and longevity. A little over a year ago, the French company with about 30 employees participated in a call for tender for the implementation of a mechanical transmission system for an F&E test bench in the area of aeronautics. The biggest names in test bench manufacturing applied for this project. BCSA offered an entirely new technical solution, which entails the integration of a torque sensor inside the transmission.
BCSA was searching for a high performance and precise torque sensor, which would take up very little installation space and would be able to cope with difficult ambient conditions. HBK offers a wide range of products in this area, which is why BCSA looked for their assistance.
HBK's strain gauge technology perfectly meets the requirements (an accuracy of 0.05% is more than sufficient). The range of torque sensors up to 45,000 rpm also satisfies the high rotational speed requirements.
The only remaining challenge was ambient conditions. The transmission system developed by BCSA is oil-cooled - an environment that had to be taken into account as well as the issue of temperature.
The main challenge was to keep the sensor within its operating temperature range.
Relevant studies and tests have proven that BCSA has developed technical solutions in which the sensor temperature will not surpass 75°C, which is more than sufficient.
There has never been an integrated solution for torque flanges with 0.05% accuracy class in this combination of torque and rotational speed (1000 Nm and 45.000 rpm) available on the market to date. Nicolas Di Pol, in charge of torque applications at HBK France explains:
"The torque sensors are among our core products and we need to continuously expand our product range to ensure that our company stays ahead of the competition in this segment. This is why we were able to quickly respond to BCSA’s request by developing a new, innovative product."
BCSA has positioned itself as a flexible, innovative company with a focus mainly on exports - a segment in which BCSA excels with up to 80% of turnover attributed to exports. The technical development of the BCSA transmission system has far surpassed standard specifications to stay ahead of the competition and most importantly - to ease the workload of the customer.
It is important to remember that power test benches (e.g. for airplane or race car motors) require a physical simulation of real conditions and of the actual loads a motor will be subjected to in order to correctly test the motor during its acceleration and deceleration processes.
Loads are generally simulated using an electric motor in generator and/or brake mode. In most cases, a mechanical transmission is implemented between the motor (running at a very high speed) and the load running at a lower speed.
The test benches are equipped with test and measurement equipment including at least one torque sensor to measure motor performance. The torque sensor will usually be positioned at the side that rotates at high speed, located between the turbo transmission and the test specimen.
David Montillet, Managing Director of BCSA, offers some insights: "Usually, the test bench integrator will implement the integration of the torque transducer in the drive train at the input of the transmission.
A prerequisite is that two additional mechanical couplings plus a torque flange have to be installed in the shaft. That means that a lot more space is needed. Aligning the shafts requires specific expertise, otherwise vibrations and mechanical loads might develop which could result in damage to the test bench. In our case, there is another challenge to overcome: rotational speed! At high rotational speeds, adding mechanical masses and components will increase the risk of vibrations which, in the worst case, may result in destruction of the test bench.
Our customer was well aware of these issues, which is why our ready-to-use solution with its turbo transmission-integrated torque sensor closed the deal ..."
"When BCSA contacted us, we had not yet developed a sensor matching their requirements but we were very interested as the demand in the market is very high. In my experience, the integration of test benches focuses mainly on monitoring and all the electronics involved, while the mechanical portion is left out. The higher the rotational speeds tested, the more the integration becomes a task for specialists. BCSA's suggestion to integrate the 1 kNm T40HS torque sensor inside the transmission offers a very promising strategy for the future", explains Nicolas Di Pol. This implementation is particularly suited to high speeds and HBK feels that it will increase the demand for high rotational speed torque sensors, specifically for airplane engine test benches. Motors run with ever increasing speeds to reduce weight - and therefore fuel consumption.
BCSA has been specializing in mechanical force introduction systems for 50 years. The implementation of reduction/turbo transmissions for test benches like the ones introduced here, represents one of the company’s core activities.
This development represents a new technological breakthrough. It puts us ahead of the competition in the current market - and in order to stay one step ahead, we will take the time we need to protect our innovations.
The torque sensors are among our core products and we need to continuously expand our product range to ensure that our company stays ahead of the competition in this segment. This is why we were able to quickly respond to BCSA’s request by developing a new, innovative product.
This will bring together HBM, Brüel & Kjær, nCode, ReliaSoft, and Discom brands, helping you innovate faster for a cleaner, healthier, and more productive world.
This will bring together HBM, Brüel & Kjær, nCode, ReliaSoft, and Discom brands, helping you innovate faster for a cleaner, healthier, and more productive world.
This will bring together HBM, Brüel & Kjær, nCode, ReliaSoft, and Discom brands, helping you innovate faster for a cleaner, healthier, and more productive world.
This will bring together HBM, Brüel & Kjær, nCode, ReliaSoft, and Discom brands, helping you innovate faster for a cleaner, healthier, and more productive world.
This will bring together HBM, Brüel & Kjær, nCode, ReliaSoft, and Discom brands, helping you innovate faster for a cleaner, healthier, and more productive world.
This will bring together HBM, Brüel & Kjær, nCode, ReliaSoft, MicroStrain and Discom brands, helping you innovate faster for a cleaner, healthier, and more productive world.