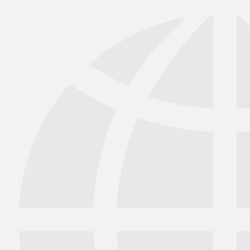
The strength behavior of components is influenced by their existing residual stresses that don't show any visible signs. Therefore, the aim is to determine the mechanical stresses in the components. With the hole-drilling method for determining residual stresses, a small hole of 1.6mm diameter is drilled into the workpiece, and strain gauges are used to measure the resulting strain.
SINT Technology and HBK offer both the MTS3000 system and the required amplifier QuantumX which enable this process to be implemented easily. The system uses a stepping motor that allows drilling at 350,000 rpm. The strain changes arising due to the step-by-step drilling of the hole into the work piece will be detected by strain gauge rosettes specifically designed for this process. Signal processing is performed digitally.
In addition to system control functions, the software package comprises four different evaluation algorithms that enable the mechanical stresses to be computed from the measured strain. The entire measurement process is PC-controlled, ensuring a high degree of measurement reliability and optimum reproducibility.
The reprocessing software allows the residual stresses in the material to be calculated from the measured strains. The choice of back calculation method is very important in producing the most accurate representation of the real stress state. Many researchers have contributed, and continue to contribute, to the extensive literature describing the hole drilling method. Currently, four different back calculation methods exist in the reprocessing software: the Uniform Stress Method according to ASTM E837-13 standard, the Non-Uniform Method according to ASTM E837-01 standard, the Schwarz- Kockelmann’s Method and the Integral Method.
This method, described in the ASTM E 837-01 standard, is based on the assumption that stresses do not vary with distance from the specimen’s surface. For this reason, the method does not consider spatial resolution. Nevertheless, when measured residual stresses are close to uniform stress field, this is the best method to choose, because it is the least sensitive to the effects of test errors. It provides also a fast estimate of the average residual stress level into the specimen; that’s why this type of calculation is universally used and accepted.
This method, described in the ASTM E 837-13 standard, introduces the computation of non-uniform stresses. Calculation steps and depth are fixed by this standard, and the calculation process refers to the Integral Method (see below for further details) with Tikhonov regularization to reduce the random errors in the calculated stresses. The ASTM E 837-13 is the only complete standard on residual stresses available at world level.
Kockelmann’s method is based on the theory that there is a correlation function between the strain derivative and the stress distribution, expressed as a function of the hole’s depth. The bond is formed by a pair of coefficients (Kx and Ky), calculated on a simulation model, that relate stress and strain. From these stress values it is possible to calculate the principal stresses and angle by using Mohr’s Circle.
This method, proposed by G. S. Schajer, provides a separate residual stress analysis at every hole-drilling depth increment. In this method, the contributions to the total measured strain relaxations of the stresses at all depths are considered simultaneously giving a higher spatial resolution than the other methods.
To simplify the problem of residual stress evaluation, Schajer proposed that the stress field could be described by means of step-wise functions whose value is constant through the partial hole depths. Using this hypothesis, Schajer established the numerical coefficients that are used for the calculation. The maximum depth that the method can be used for is 0.5 times the mean radius of the strain rosette used for the test.
The integral method should be chosen when residual stresses are expected to vary significantly with depth; however, it also has the highest sensitivity to test errors.
As a leading company in measurement and testing, the mission of SINT Technology is to offer tailor-made solutions to its customers.
When flexibility is needed, we provide support to companies operating worldwide in several industrial sectors, ensuring quality of services, fast response and the expertise of our technicians.
SINT Technology is a trusted partner and a centre of excellence recognized by the Italian Accreditation Body ACCREDIA.
Continuous improvement in research and innovation make our solutions the state of the art in experimental testing and in the production of measurement systems.
This will bring together HBM, Brüel & Kjær, nCode, ReliaSoft, and Discom brands, helping you innovate faster for a cleaner, healthier, and more productive world.
This will bring together HBM, Brüel & Kjær, nCode, ReliaSoft, and Discom brands, helping you innovate faster for a cleaner, healthier, and more productive world.
This will bring together HBM, Brüel & Kjær, nCode, ReliaSoft, and Discom brands, helping you innovate faster for a cleaner, healthier, and more productive world.
This will bring together HBM, Brüel & Kjær, nCode, ReliaSoft, and Discom brands, helping you innovate faster for a cleaner, healthier, and more productive world.
This will bring together HBM, Brüel & Kjær, nCode, ReliaSoft, and Discom brands, helping you innovate faster for a cleaner, healthier, and more productive world.
This will bring together HBM, Brüel & Kjær, nCode, ReliaSoft, MicroStrain and Discom brands, helping you innovate faster for a cleaner, healthier, and more productive world.