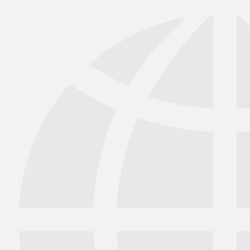
When designing an electric motor drive system, no matter what the application is, there are three elements:
Often, these elements come in the form of a battery acting as a DC Bus – an inverter which changes the DC power to AC power – and a motor which uses the AC power to convert electrical energy into mechanical power. This is sometimes referred to as electro-mechanical power conversion.
In this article, Mitchell Marks explains the basics and requirements for testing electrical inverters and machines. What he likes about this application:
"Motors took over the industrial world for 100 years without having any ability to control them because they were clean and reliable, just plug them in and they go. Now that we have the ability to control them they are being integrated everywhere from cell phones to submarines. With so many applications the work will never end and no day will ever be the same."
The history of the math for controlling and understanding the induction machine took about 50 years for people to solve. It is amazing that we were using the machine 50 years before we could understand it!
At the end of the day, most applications have size restrictions and cost restrictions, which determine many of the variables before motor design even begins.Hence, we have the choice of topology and small details, based on the control scheme that groups want to use. There are also choices that can be made with cooling, and how the motors are wound. The main types of motor are induction, permanent magnet, wound field, and switched reluctance. Induction motors are the easiest to control, we understand them the best, they are a total workhorse of industry; however, their downside is that the field needs to be excited, which results in losses. Permanent magnet (PM) motors are used a lot in applications where efficiency is important and size is a restriction, as they have a higher Power Density because the magnet supplies the rotor field rather than having the losses in the rotor These PM motors require an inverter and a lot of cooling and care when operating in different modes. They also have the down-side of losing out on Constant Power Speed Ratio CPSR, because the field cannot be weakened as easily. Field weakening is a method of reducing the rotor’s magnetic field in order to increase the speed of a machine. We can weaken the field in the Induction Machine or PM machine by injecting q-axis current. The need to have controlled amounts of q axis (used to control torque) or d axis (used to control rotor field) current for FOC is a reason why many groups are interested in monitoring their dq0 plots in real time. With a PM machine more considerations need to be taken because the magnets can become demagnetized during field weakening and back emf may need to be monitored. Synchronous Reluctance (SR) motors have a very simple rotor which is simply a lamination with a specific pattern. These motors use the property of reluctance torque in order to create rotational motion. These motors are very useful in a variety of applications because of their simple construction but have the downside of creating a large amount of noise and vibration. For this reason they have only been used in specific scenarios. During testing of these machines, researchers are mainly interested in having a vibration map of what torque and speed vibrations are the strongest.
The cooler the motor, the less the losses; the less the losses, the higher the efficiency.Additionally, if magnets get too hot, they can demagnetize in certain regions, which can be very bad. Hence, keeping the windings and switches cool is very important. Switches will have higher losses and can also explode if they get too hot. Researchers spend a large amount of design time on exploring cooling strategies to make their machines more efficient. Cooling systems are often water, oil, or glycol pumped and sprayed over the areas that it is desired for heat to be removed. The stress on cooling machines has made motor temperature monitoring an important part of operation and testing. A test will have thermocouples for monitoring temperatures which are logged or sent to a control system for shutdown. Having these logged values synchronized with the data would be of interest for researchers to know when and where temperature changes happened in response to their controls. This is another area where data can be used for model validation.
The best way of covering many of the above mentioned topics is efficiency mapping and dyno testing or dynamometer testing. Everybody wants to increase the efficiency of their systems. Having the raw data is important for this, because if something goes wrong you can reference previous tests and also perform in-depth analysis in a post processing program such as nCode GlyphWorks or MATLAB. Furthermore, this is of the utmost importance for dynamic testing, because when carrying out dynamic loading or testing drive cycles, if you don’t have the raw data, you can get some weird inaccurate efficiencies.
When they start testing they will have a set DC bus voltage, followed by a set speed.
They will then load the machine with a certain torque. You will do this for all of the desired torques and speeds available in the range of the machine. This will then give you the efficiencies for all desired set points, and you obtain an efficiency map. These points will be taken at a specific temperature range. Sometimes you have to wait for the machine to cool down in order to take a measurement at a set point. This is where HBM’s eDrive testing system can save a lot of time for customers because taking test points in a number of cycles rather than a number of seconds will have the machine spending less time heating up.
Often, people will test the limits of the machine, and basically blow them up; or attempt to. They will push to achieve the maximum speed to know the mechanical limits of their machine. The ability to trigger and have a buffer of data will allow researchers to understand not only where their machine failed but how it failed.
This will bring together HBM, Brüel & Kjær, nCode, ReliaSoft, and Discom brands, helping you innovate faster for a cleaner, healthier, and more productive world.
This will bring together HBM, Brüel & Kjær, nCode, ReliaSoft, and Discom brands, helping you innovate faster for a cleaner, healthier, and more productive world.
This will bring together HBM, Brüel & Kjær, nCode, ReliaSoft, and Discom brands, helping you innovate faster for a cleaner, healthier, and more productive world.
This will bring together HBM, Brüel & Kjær, nCode, ReliaSoft, and Discom brands, helping you innovate faster for a cleaner, healthier, and more productive world.
This will bring together HBM, Brüel & Kjær, nCode, ReliaSoft, and Discom brands, helping you innovate faster for a cleaner, healthier, and more productive world.
This will bring together HBM, Brüel & Kjær, nCode, ReliaSoft, MicroStrain and Discom brands, helping you innovate faster for a cleaner, healthier, and more productive world.